Andon
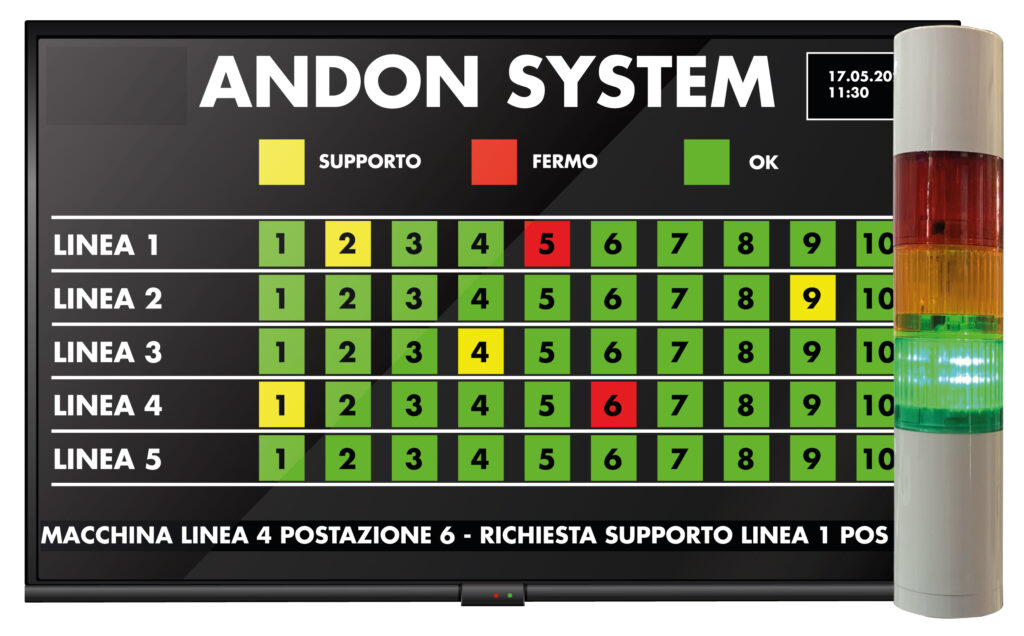
L’Andon è un apparecchio luminoso che segnala lo stato di funzionamento di una macchina o di un processo produttivo. Il termine è giapponese, e si riferisce alle lanterne che venivano agitate per segnalare qualcosa come l’arrivo o la partenza di un veicolo.
L’andon fa parte della gestione a vista dei processi e posti di lavoro di una lean organization, è montato sulle apparecchiature o in prossimità di esse, è azionato da pulsanti manuali o da dispositivi elettronici dai lavoratori addetti all’apparecchiatura, che hanno la facoltà di interrompere il processo di produzione ogni volta che rilevano un problema di qualità del prodotto o di processo di produzione. I singoli segnalatori sono collegati ad un tabellone che raccoglie i segnali luminosi che indicano quale stazione ha il problema.
L’operatore ferma l’impianto e chiede assistenza se riscontra l’esaurimento di componenti, un difetto creato o rilevato, malfuzionamento di attrezzatura o un problema di sicurezza. Il lavoro viene sospeso fino a quando non viene trovata una soluzione. Gli allarmi possono essere registrati in archivi dati per poter essere studiati durante i programmi di miglioramento continuo.
I sistemi moderni oltre ai segnali luminosi possono inviare messaggi di testo e segnali sonori.
Ogni operatore dovrebbe avere a disposizione una pulsantiera o anche una semplice corda che accende una luce e consente di bloccare e riavviare la lavorazione. Nei sistemi più avanzati è la macchina stessa che, dotata di appositi sensori, accende la luce e si ferma se rileva anomalie. Sempre in modo automatico invia messaggi di notifica che poi vengono archiviati.
Il sistema andon serve a migliorare la comunicazione fra gli operatori di produzione, i team leader o i tecnici esterni in caso di problemi di produzione. Il concetto di base, “fermare la linea” non appena viene rilevato un difetto del prodotto, mira a ridurre la probabilità di trasferire il difetto lungo il resto del processo, in base al principio che risolvere i problemi a monte è più economico che affrontarli a valle o lungo tutto il percorso.
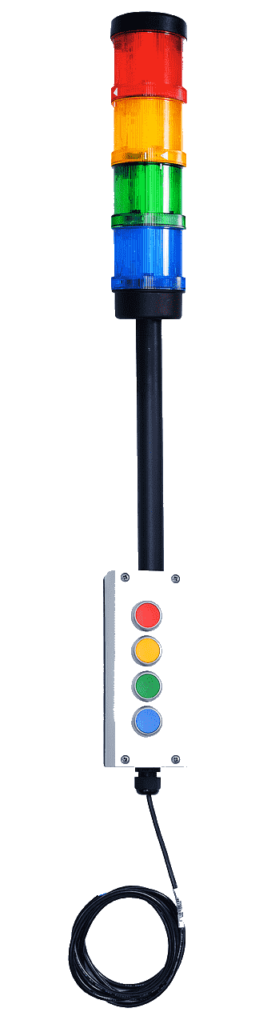
I colori di base di andon sono, come per i semafori, verde, giallo e rosso. Il verde significa che tutto va avanti normalmente. Il giallo indica che è stato rilevato un problema ancora piccolo, ma che potrebbe ingrandirsi se trascurato. Non c’è bisogno di fermare la linea, basta prendere atto del problema. Ogni volta che appare una luce gialla sull’andon board o su un altro sistema, un manager o un team leader dovrebbe recarsi alla workstation e aiutare ad affrontare prontamente il problema. Il rosso invece segnala che è stato rilevato un problema di produzione o un difetto tali da dover fermare l’impianto fino a quando il problema non viene risolto. Ogni volta che accade, tutti gli operatori vanno alla stazione che ha il problema e discutono in merito alle possibili soluzioni.
Alcuni sistemi, come quello manuale che si vede nella foto, hanno una luce blu che significa esaurimento di materie prime o componenti per la lavorazione.
Andon può essere usato anche al di fuori della produzione, per sistemi di magazzino, logistica e customer satisfaction.
Attraverso andon, le aziende non scendono a compromessi sulla qualità del prodotto, anche se ciò significa rallentare l’intera produzione per un certo periodo. In un primo momento, questo può rivelarsi controproducente, tuttavia garantisce una maggiore efficienza del team e la soddisfazione del cliente a lungo termine. Al proposito i lavoratori sono spinti ad usarlo senza remore, perché è meglio segnalare un piccolo difetto invece di ritrovarsi con un problema più grosso.
Con andon si hanno diversi benefici.
- Minori costi di produzione: Andon aiuta le aziende a cogliere i problemi di produzione all’inizio del processo e ad evitare che i prodotti difettosi si protrarranno ulteriormente lungo la linea di produzione, riducendo rilavorazioni e costi.
- Minori problemi ricorrenti: quando una linea viene fermata, gli operatori vanno nel punto in cui è stato rilevato il problema per trovare la causa principale, riducendo la probabilità che si ripresenti.
- Miglioramenti continui e soddisfazione del cliente: grazie al fatto che va alla radice del problema, i team del lean manufacturing cercano di migliorare continuamente i loro processi con cui si otterrà maggiore qualità dei prodotti e soddisfazione dei clienti.
- Tempi di consegna più rapidi con un flusso regolare attraverso la linea di produzione. L’eliminazione dei problemi alla radice riduce i periodi di fermo migliorando i tempi di consegna.
- Miglior flusso di informazioni con messaggi inviati a divisioni esterne, in modo che restino vigili ogni qualvolta che si verifica un problema di produzione.